05 | 2012 – Built-in measurement technology enhances the reliability of manufacturing optical components
New broadband spectral measurement technology is allowing direct and more precise monitoring of high-rate deposition of optical multilayer systems
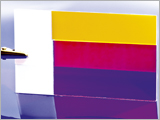
The surfaces of precision mirrors for laser technology, optical filters for displays, and for other complex optics consist of multiple layers of transparent materials with high and low refractive indices. The requirements on the precision regarding deposition of the individual layers are extremely high: For example, layer thickness deviations must be less than one nanometer for many applications. In order to deposit these layer systems on large areas and under industrial conditions in a very precise and reproducible way, new sputter processes have been developed whose key advantages are their high productivity and also their high versatility with regards to the materials that can be deposited, to the layer design, and to layer properties.
In order to compensate in real-time for small unavoidable deviations in the layer thickness that occur during the coating process, in-situ measurement systems are required. The rates of measurement and analysis of these systems has to be sufficient for high coating rates (typically 3 nm/s) and the systems must simultaneously provide all necessary information about the layer growth. Working together in the OptiLaySens project (Optical in-situ process sensor technology for high-rate production of optical multilayer systems), the medium-sized measurement technology developer LayTec AG, the optics software developer W. Theiss Hard- and Software, and the Fraunhofer Institute for Electron Beam and Plasma Technology FEP have developed a method for real-time monitoring of the layer growth and for adjusting the actual coating process to compensate for any deviations. LayTec AG developed the spectral measurement system as well as new evaluation algorithms. The measurement system was integrated into industry-like sputter plants at the Fraunhofer FEP and was optimized for demanding coating systems. The result was a fully automatic coating module, suitable for coating substrates of up to 200 mm diameter via pulse magnetron sputtering at high deposition rates of 3 nm/s. The engineering office W. Theiss Hard- and Software developed optimum algorithms for the evaluation and for compensation of process fluctuations.
In contrast to the single wavelength methods used so far, the new method can measure a full reflection spectrum of the surface up to the UV region in a fraction of a second. This allows measurement of even thin individual layers, which are increasingly part of demanding layer systems. During the actual coating process information about the layer thickness is obtained from the reflection spectrum. This information allows compensation of even the smallest deviations, which are unavoidable during the coating process. A software algorithm, developed as part of the project, calculates the required corrections during the coating process for the subsequent layers of the multilayer system. Moreover, it translates this into specific process parameters in order to compensate the layer thickness deviations.
The rapid recording of the layer thickness during the coating process and immediate adjustment of the process parameters for subsequent layers were tested on two leading-edge applications under near-industrial conditions. These were namely the deposition of broadband antireflection layer systems and of optical edge filters. The research team achieved very high precision of the optical properties of ± 1% and a layer thickness accuracy of ± 0.5%. The real-time compensation of high-rate sputter processes thus contributes to improved processing reliability and minimization of production rejects in the industrial production of optical components.
About OptiLaySens:
The OptiLaySens project was a joint project conducted by LayTec AG (Berlin) and the Fraunhofer Institute for Electron Beam and Plasma Technology FEP (Dresden). The Federal Ministry of Education and Research (BMBF) funded the project (funding ref. 13N11005, 13N11004) as part of the »SME innovation: Optical Technologies« initiative. The project lasted from the start of May 2010 to the end of April 2012.
Download the press release and picture