Coating tools directly from the 3D printer
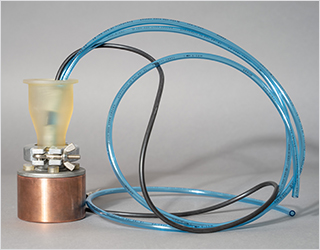
As part of an in-house research project, we were able to develop, manufacture and successfully test a functional sputtering magnetron using additive manufacturing on one of our coating systems..
There are many requirements for the materials used in a magnetron. They must withstand and dissipate the heat generated at the target, withstand the pressure gradients within the system, and be able to isolate high voltages. These requirements are well-known for parts when produced by machining. For additive manufacturing, these properties are often still unknown and depend highly on the printing parameters. In the course of the project, various methods such as stereolithography, selective laser sintering, as well as laser and electron beam powder bed processes, were compared and evaluated.
After comparing the individual methods and evaluating different test specimens, a small magnetron was designed and produced using additive manufacturing. The production was carried out in collaboration with local companies and other Fraunhofer institutes. For the final demonstrator, all metallic parts, all insulators as well as most of the magnets were printed. We were able to not only make the magnetron even more compact, but also reduce the number of parts by, for example, directly integrating cooling channels into the main body. The use of additive manufacturing also led to a drastic reduction in production time. The post-processing of the individual parts took place in-house.
The project was completed with a practical test, where we were able to successfully deposit copper. We want to continue using the new possibilities of additive manufacturing in the future to incorporate further functionalities into our key components, such as highly efficient cooling structures, complex magnetic geometries, and many more.