Laboratory coater for 3D layer deposition by means of pulse magnetron sputtering
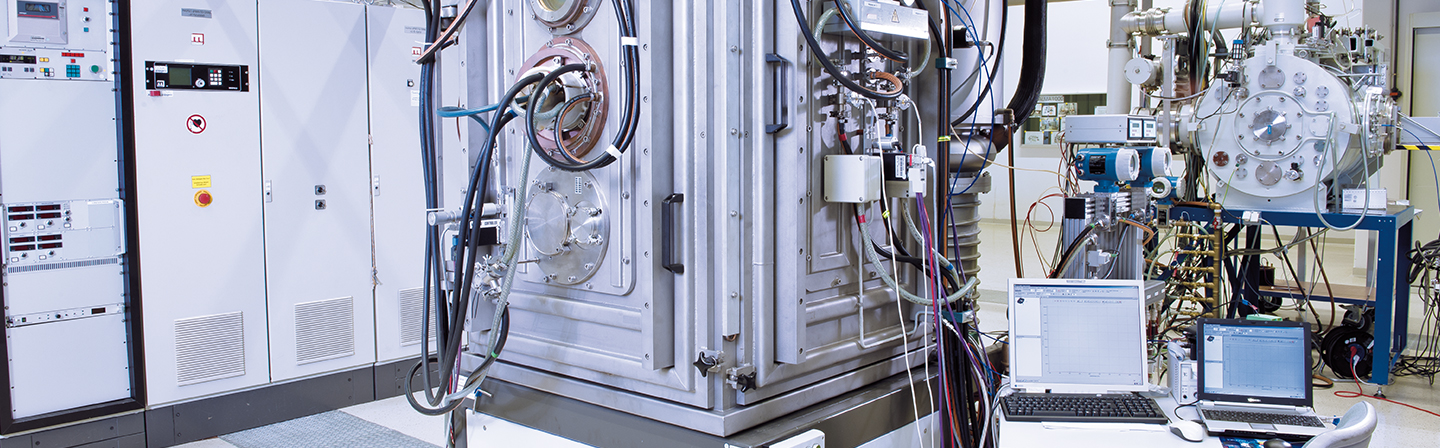
One of the business units at Fraunhofer FEP develops technologies for the coating of shaped substrates with non-planar geometry.
Depending on the type of coating, the corrosion, scratch or wear resistance of components can be increased. Decorative appearance and other specific functionalities can also be realized by selecting suitable coating materials.
In our experimental plant, UNIVERSA, we can process components of any material.
The technological setup enables plasma pre-cleaning (plasma etching) of the components, sputtering of adhesion promoting layers as well as coating by high-performance pulse sputtering processes.
For the deposition of various metallic or non-metallic coating materials, both non-reactive and reactive coating methods can be used.
One main focus of our work is the optimization of technological processes and substrate handling for component treatment in order to adapt the functionality of the coating to the requirements of the application and the substrate properties.
The advantage of vacuum coating compared to conventional wet-chemical or metallurgical coating processes for components lies in the achievable high layer quality and the wide range of layer structures that can be produced. Environmental soundness and cost efficiency are further benefits of the technology.
Coating chamber | 1500 l-batch-coater with rotary substrate holder and substrate heater |
Coating modules | 4 magnetron sources |
Target dimensions | 512 × 128 mm2 |
2 sputter pulse power supplies | 60 kW, 1000 V, max. 1000 A pulse current at up to 50 kHz pulse frequency |
Pulse power supply for etching and bias | 20 kW, 1000 V, max. 60 A pulse current at up to 33 kHz pulse frequency |
Hollow cathode module | 200 A |
Max. substrate dimensions for 400°C-technology | ca. 500 × 500 × 500 mm3 |
Max. substrate dimensions for 700°C-technology | ca. 150 × 70 × 70 mm3 |
Computer-controlled operation and data acquisition |